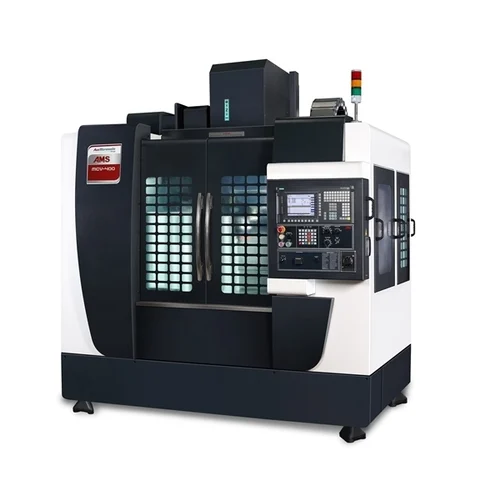
Vertical Machining Centers (VMC) have transformed manufacturing, allowing precise machining of diverse materials. One often-overlooked but vital component of VMC machines is clamping elements. These seemingly simple devices play a pivotal role in ensuring accuracy, efficiency, and safety during machining. In this article, we’ll explore the world of clamping elements for VMC machines, including their types, functions, and significance in the machining process.
Types of Clamping Elements
- T-Slot Nuts: These are commonly used clamping elements in VMC machines. T-slot nuts fit into the T-slots on the machine table, providing secure fastening for workpieces and fixtures. They come in various sizes to accommodate different workpiece dimensions.
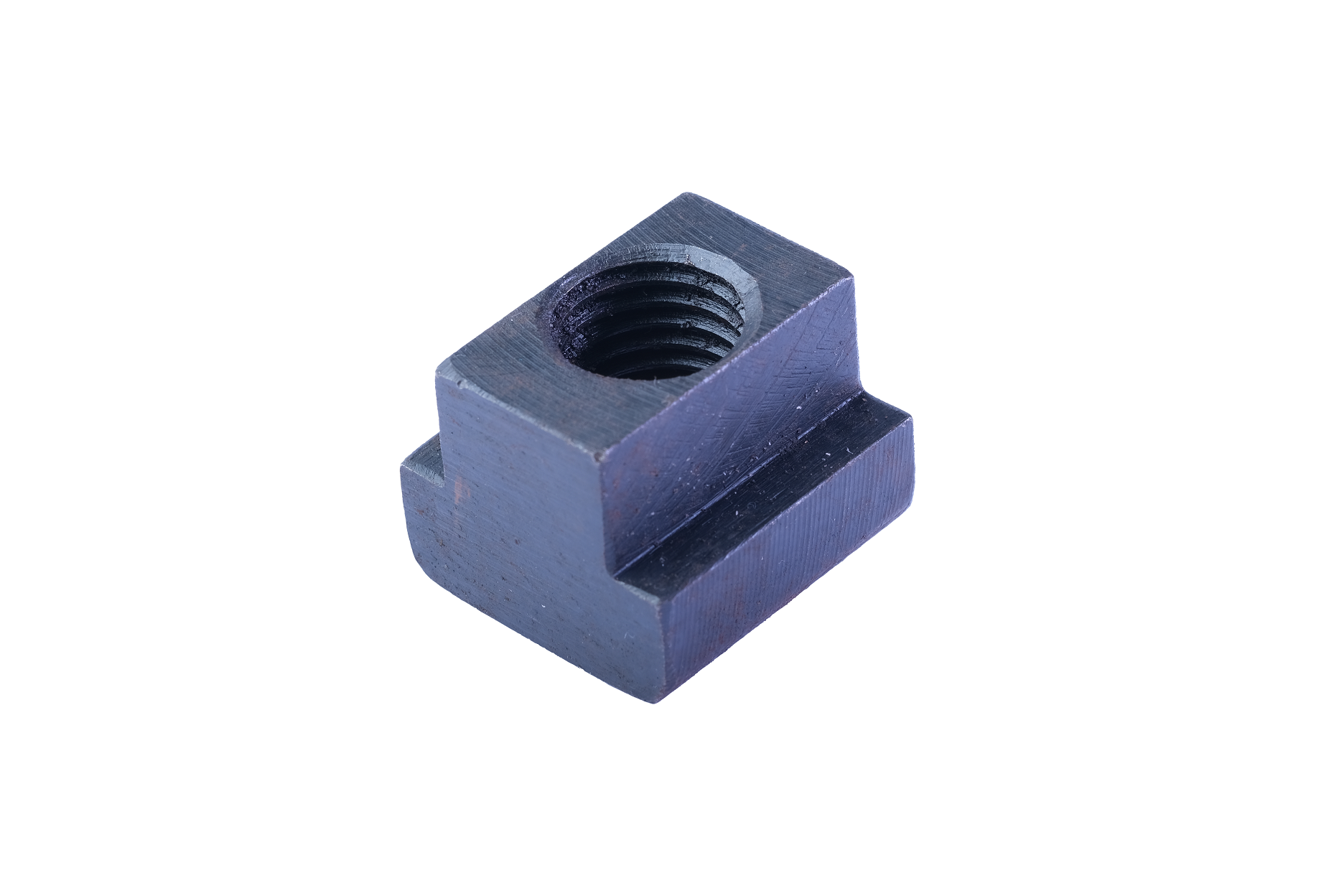
- Clamps: Versatile clamping elements that secure workpieces during machining. They come in various configurations, such as strap clamps, toe clamps, and edge clamps, offering flexibility for diverse machining needs.
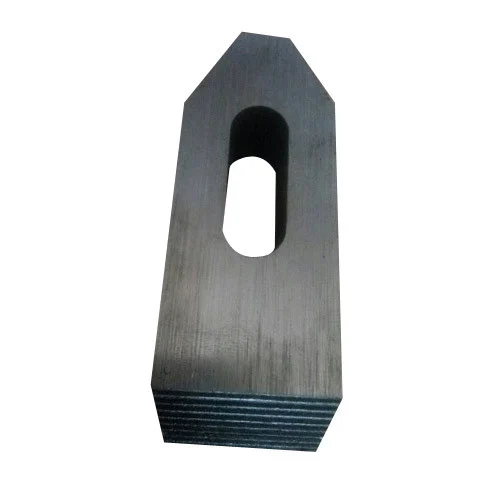
- Vices: Precision clamping devices designed for securely holding workpieces, especially when machining multiple sides of a workpiece in a single setup. VMC machines often feature dedicated vice fixtures.
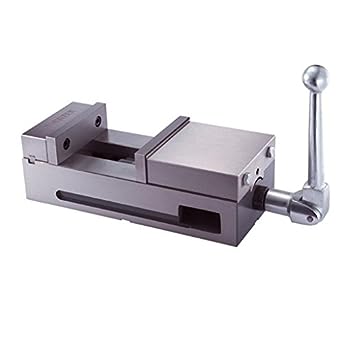
- Fixture Plates: These customizable clamping elements allow you to create specific setups for holding workpieces. Fixture plates come with a grid of holes for attaching various clamping components, making them highly adaptable.
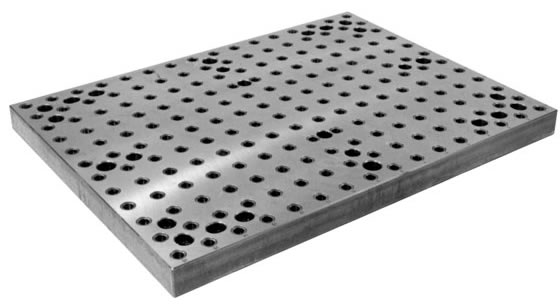
Functions of Clamping Elements in VMC Machines
- Workpiece Stability: Clamping elements primarily secure workpieces in place, preventing vibration, movement, or shifting during machining. This stability ensures precise cuts and accurate dimensions.
- Safety: Properly clamped workpieces enhance the safety of VMC machine operations, reducing the risk of accidents caused by loose or uncontrolled workpieces.
- Reduced Setup Time: Clamping elements, especially fixture plates, simplify the setup process, allowing quick and repeatable positioning of workpieces and fixtures, reducing downtime and setup errors.
- Enhanced Machining Efficiency: These elements enable machining multiple workpieces in a single setup, minimizing the need for frequent workpiece changes. This leads to improved machining efficiency and reduced production costs.
- Precision Machining: Clamping elements significantly contribute to the overall accuracy of VMC machining by maintaining consistent workpiece positioning, minimizing errors, and ensuring high precision in the finished parts.
Importance of Choosing the Right Clamping Elements
Selecting the appropriate clamping elements for your VMC machine is crucial for optimal results. Consider:
- Workpiece Material: Different materials require specific clamping solutions to prevent deformation or ensure stability.
- Workpiece Size and Shape: The type and configuration of clamping elements should match your workpiece dimensions and geometry.
- Machining Operations: Specific operations may require specialized clamping solutions, such as vices for multi-sided machining or custom fixtures for unique workpieces.
- Repeatability: For frequent production of similar parts, opt for clamping elements that offer high repeatability, streamlining your processes.
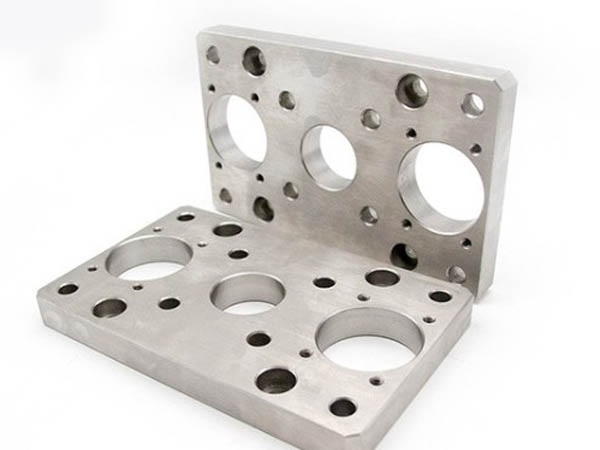
Conclusion
Clamping elements may not steal the spotlight in VMC machines, but they are the unsung heroes enabling precision, efficiency, and safety in machining operations. Choosing the right clamping elements and using them effectively can make a significant difference in the quality and productivity of your machining processes. Understanding their types, functions, and importance is the first step toward harnessing their full potential in your manufacturing operations.